گریس
گریس یکی از روانکنندههایی است که از زمانهای دور برای روانکاری مورد استفاده قرار میگرفت. انواع گریس دربازار موجود است که آن را بر مبنای نرمی، زبری و ... دستهبندی میکنند. در ادامه با مفهوم کلمه گریس آشنا خواهیم شد.
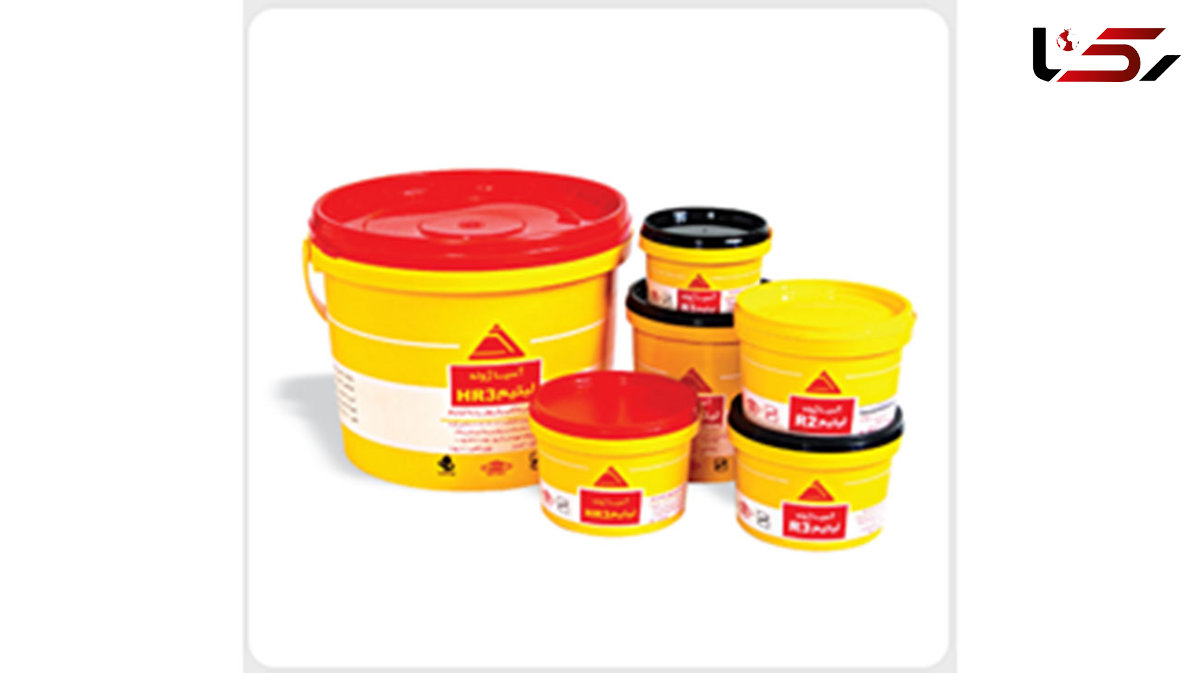
گریس چیست؟
به مادهای جامد یا نیمه جامد که دارای گرانروی زیادی باشد و از مشتقات ترکیبی صابون یا نفت ایجاد شود را گریس میگویند. در ساختار گریس از پرکنندههایی استفاده میشود تا هنگامی که از آن در قطعات متحرک و با فشار زیاد استفاده میشود، بتواند به قطعه به خوبی چسبیده و از آن جدا نشود.
واژه گریس از لغت لاتین کراسوس به معنی چربی الهام گرفته شده است. نخستین گریسهای تولید شده بر پایه کلسیم بوده است که از ترکیب مواد به صورت سرد به دست میآید. نوع دیگر گریس نیز گریس سیلیکون نام دارد و همان طور که از نام آن پیدا است، پایه این نوع از گریس ها سیلیکون است.
مواد تشکیل دهنده گریس
گریس از ترکیب سه ماده اصلی روغن، غلیظ کننده و افزدونیها تولید میشود که در ادامه به بررسی هر کدام از آنها خواهیم پرداخت:
روغن
اکثر گریسهای موجود در بازار از روغن معدنی که از نفت مشتق شده است، به دست میآیند. این روغن میتواند در هر دو دمای بالا و پایین به خوبی طاقت آورده و عملکرد خوبی در کاربردهای صنعتی داشته باشد.
غلیظ کننده
غالبا از مادهای که اصطلاحا به آن صابون فلزی گفته میشود، به عنوان غلیظکننده استفاده میشود. غلیظ کننده مادهای است که در ترکیب با روغن، ساختار جامد نیمهرسانا تولید میکند.
صابون فلزی و یا Metalilic soap از لیتیوم، آلومینیوم، پلی اوره، کلسیم، سدیم و خاک رس ساخته شده است.
گریسهای جدید و امروزی این روزها به دلیل تحمل دما و فشار بالاتر از محبوبیت بیشتری برخوردار شدهاند. به این غلیظ کنندهها، غلیظکنندههای پیچیده گفته میشود.
این نوع گریسها از ترکیب صابون فلزی با یک عامل پیچیده به دست میآیند که عموما این گریسها بر پایه لیتیوم است.
البته در نظر داشته باشید برای استفاده درمحیطهای با درجه حرارت بسیار بالا از غلیظ کنندههای بدون صابون استفاده میشود. به عنوان مثال: بتونیت و سیلیس دو نمونه از غلیظکنندههای بدون صابون میباشند که در حرارت و دمای بالا ذوب نمیشوند.
افزدونیها
افزدونیها به دلیل خاصیتی که دارند باعث میشوند تا خواص مثبت و خوب گریس افزایش پیدا کرده و خواص منفی و نامطلوب آن کاهش پیدا کند. از شایعترین مواد افزودنی گریس میتوان به جلوگیری از اکسیداسیون یا زنگ زدن و همچنین عامل کاهش اصطکاک اشاره کرد.
کاربرد گریس
گریس غالبا در شرایطی که امکان استفاده از روانکننده مایع وجود نداشته باشد و یا مقرون به صرفه نباشد مورد استفاده قرار میگیرد. از عمدهترین تفاوتهای گریس با روانکننده میتوان به این مورد اشاره کرد که گریسها پایه خنککنندگی و پاککنندگی ندارند.
جالب است بدانید استفاده از گریس در مسائل صنعتی و استفاده از نیروهای محرکه نظیر یاتاقان و یا بلبرینگ بسیار مورد استفاده است.
از عمدهترین مصارف گریس میتوان به موارد زیر اشاره کرد:
- استفاده از گریس در روانکاری ماشینآلاتی که تحت دما و فشار بالا میباشند، بسیار رایج است.
- گریس به دلیل ماندگاری و دوام بالایی که دارد باعث افزایش طول عمر قطعه میشود.
- روانکاری در مجاورت آب با گریس قابل حل است.
- در ماشینآلاتی که برای کار بهتر نیاز به روانکننده دارند و قابلیت روانکاری و روغنکاری به طور دائم نداشته باشند، میتوان از گریس درمدت طولانی استفاده کرد.
- گریس بر روی سطح میماند و یک لایه روانکننده همیشه بر روی سطح قطعه موجود است که این امر برای ماشینآلاتی که به طور متناوب مورد استفاده قرار گرفته و یا مدت زمان طولانی روی حالت استندبای قرار میگیرند، بسیار مناسب است.
مزایای گریس
- کاملتر شدن آببندی سیستمها، کاهش نشتی و چکهکردن روانکننده.
- سادگی طراحی سیستمهای روانکاری.
- ماندگاری بالا در محل روانکاری شده.
- سهولت مصرف و کاهش دفعات روانکردن قطعه و یا سیستم.
- بهینهسازی چسبندگی به قطعات، حتی در شرایطی با فشار و دمای بالا.
معایب استفاده از گریس
درست است که استفاده از گریس دارای مزایای زیادی است اما به نسبت سایر روان کنندهها دارای معایبی نیز است.
از جمله مهمترین معایب استفاده از گریس میتوان به موارد زیر اشاره کرد:
- مشکل در انبارداری و عدم سهولت در بستهبندی.
- گریس دارای قابلیت خنککنندگی بسیار پایین است.
- عدم امکان پاک کردن و تمیز نمودن آلودگیها از سطح قطعات متحرک در هنگام استفاده از گریس.
- نیاز به نیروی کار بیشتر برای روانکاری کردن.
- گریس قابلیت نفوذ و وارد شدن به قطعات ریز و مجاری دستگاهها را ندارد.
درآخر
درست است گریس دارای معایب زیادی است اما نیاز به گریس را نمیتوان انکار کرد، امروزه استفاده از گریس به عنوان روانکننده در بسیاری از صنایع و نیروهای محرکه رایج است که نبود آن باعث مشکلات و بعضا خرابیهای سیستمهای متحرک میشود و میتواند خسارات جبرانناپذیری را برای صاحبین صنایع داشته باشد.
اما بهتر است در انتخاب گریس دقت بیشتری نمایید و با توجه به نوع کار خود گریس مناسب را انتخاب کنید.
نوع سرعت و دمای عملیات ماشین آلات، میزان رطوبت محیط، تغییرات درجات حرارت، عمر مفید گریس، شرایط مجدد گریسکاری دستگاه و همچنین سازگاری با قطعات لاستیکی و پلاستیکی چون کاسه نمد لاستیکی از مهمترین عواملی است که باید به آن در هنگام خرید دقت کرد.
-
ساخت شگفتانگیز لامبورگینی چوبی در گاراژ خانه + فیلم
ارسال نظر